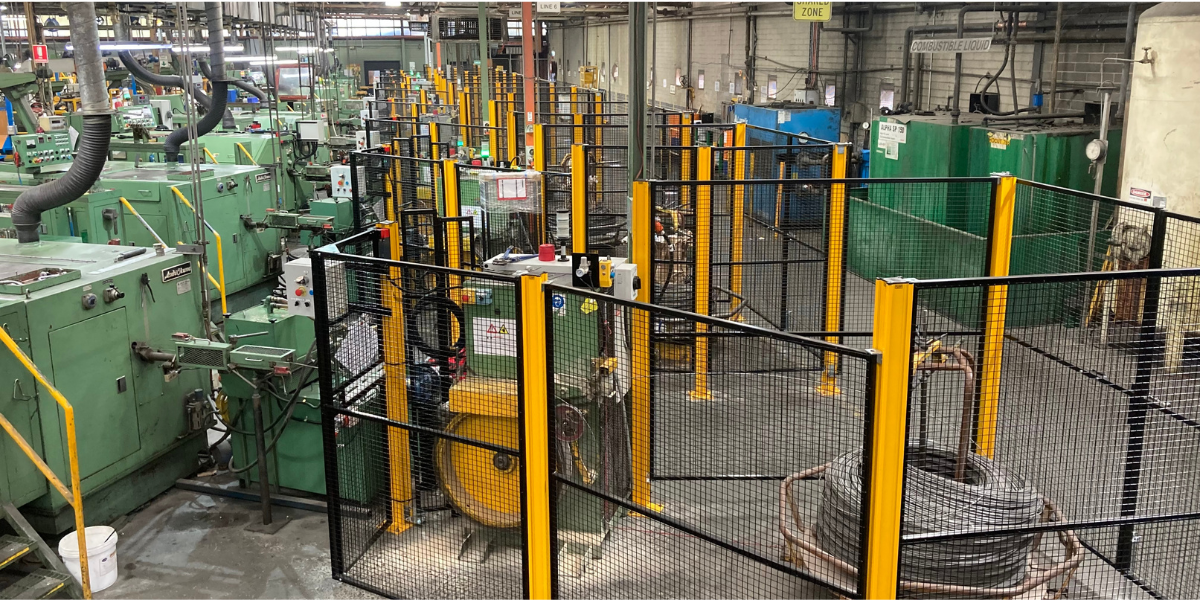
Teoma Group is a highly experienced firm realising our clients’ diverse factory automation and safety of machinery compliance needs. The team’s ability in these areas has been recognised by the National Electrical & Communication Associations winning an excellence award for the ‘work health and safety best practice’ category. The service showcased by this award was a ‘complete’ safety of machinery services solution, the basis of which offers relevance to all manufacturers. This project emerged with ITW Construction Asia Pacific’s Buildex® plant seeking to ensure that long-serving machinery remains safe and current with legislation and standards.
With several in-house CMSE® – Certified Machinery Safety Expert’s (TÜV NORD) having extensive experience in delivering safety of machinery projects, and a team of skilled industrial electrical and mechanical specialists, Teoma Group and Industrial Automation Hallam were identified for our capacity to support Buildex® with ‘complete’ safety of machinery project solutions. Buildex® has an extensive history in Australia manufacturing fasteners and building products for over 100 years with its Melbourne facility now producing up to 2 million fasteners daily. Illinois Tool Works (ITW) businesses produce product lines under names synonymous with construction in Australia including, Buildex®, Pryda, Paslode®, Ramset Reid™, Zenith® and many more.
Project Overview: Aspire 5 Production Line
Labour Hours: Approx 600hr
Client: Buildex®
Services provided:
- Safety of Machinery Consultation, Hazard Identification and Risk Assessment.
- Design and manufacture of Safety Control Systems
- Fabrication & Installation of Mechanical Guarding
- Integration of Electrical, Fluid Power, and Mechanical Safety Related Parts
- Risk Review and Validation in accordance with AS4024.
Total Machines in Project: 1x Wire Drawer, 1x Header, 1x Forge and 1x Thread Roller.
The award-winning project presented to NECA for evaluation was a holistic solution delivered on the Buildex® Aspire 5 production cell. This recognised our unique in-house capability of assisting a client with all stages of a safety of machinery project. This project commenced with our detailed record of hazard identification and risk assessment and was followed by hazard mitigation for all identified hazards and energy sources.
In completion, we oversaw final reviews, delivered training, and provided all handover documentation which included records of assessment, validation, drawings, verified programs, instructions etc. It provided a seamless project that sought all knowledge, history, and experience of the customer personnel currently or previously associated with the machinery, and importantly was inclusive at all levels through the process of considering control methods to ensure practical process-friendly safety solutions.
The safety control methods integrated were fit-for-purpose and made the best use of both common and latest technologies. Control methods included but were not limited to;
- Updated modular perimeter guarding
- Trapped key solutions
- Solenoid locks with RFID interlocks
- RFID type non-contact interlocks
- Programmable safety controllers
- Emergency stops
- Two-hand controls
- Dual monitored pneumatic safety valves
- Safety contactors
- Safe-torque-off
- Audible visual warnings
- Custom guarding
- Fit for purpose lockable isolation valves
- Labelling and identification
- LOTO placarding and information
- Safety control instructions etc.
Process Overview:
- Consult and review operational requirements.
- Carry out hazard identification and risk assessment.
- Hierarchy of control considerations for mitigating controls.
- F.M.E.A of existing engineering controls.
- Conceptual safety design for electrical, pneumatic, hydraulic and mechanical safety-related parts.
- Detailed costing.
- Design drawings.
- Design validation.
- Procure and manufacture safety control systems, fabricate guarding.
- Carry out installation and integration.
- Programming, commissioning, and verification testing.
- Isolation placarding.
- Residual risk review and assessment record update.
- As built drawing update and validation record.
- Operational instruction & client training.
- Final documentation handover.
A common industry practice can be to engage various consultants and integrators for specific tasks, which still requires a manufacturer to maintain in-house current and in-depth legislative and standards knowledge, complete with the competent technical understanding of safety-related parts of machinery for electrical, mechanical, pneumatic and hydraulic hazards. Sometimes, where this is not a seamless process, or where knowledge or skills have not been fully developed, it may result in unforeseen risks.
Getting safety of machinery right requires a particular skill set. As an example, we are often directed by a customer to ‘just add’ an additional guard switch or emergency stop to a machine. What is often not understood by others is that by ‘just adding’ a device without knowledge of safety control and its procedural requirements, can easily result in derating the category of control achieved, effect the fault behaviour and fault detection of the safety related parts, and result in a loss of reliability and compliance of the machine safety. Whilst we don’t want anyone hurt at work, who is responsible for the correct undertakings and who is responsible where they have not been followed? Those answers can be found in the legislation. Are you up to date?
The major point of difference for the service provided by Teoma Group and Industrial Automation Hallam is our proven capability and qualified skillset to deliver all steps and requirements thoroughly and seamlessly from the investment that we have made for our clients, in our maintaining of these in-house resources. This is the same level of professionalism and complete support that we offer for all of our electrical and mechanical industrial automation, installation and breakdown services which encompass our values, QA management systems and industry best practice.
The end result of our projects with Buildex® is not only aiding their personnel’s safety, and legislative compliance, but also confidently working deeper to ensure successful outcomes around safety moving forward into the future.