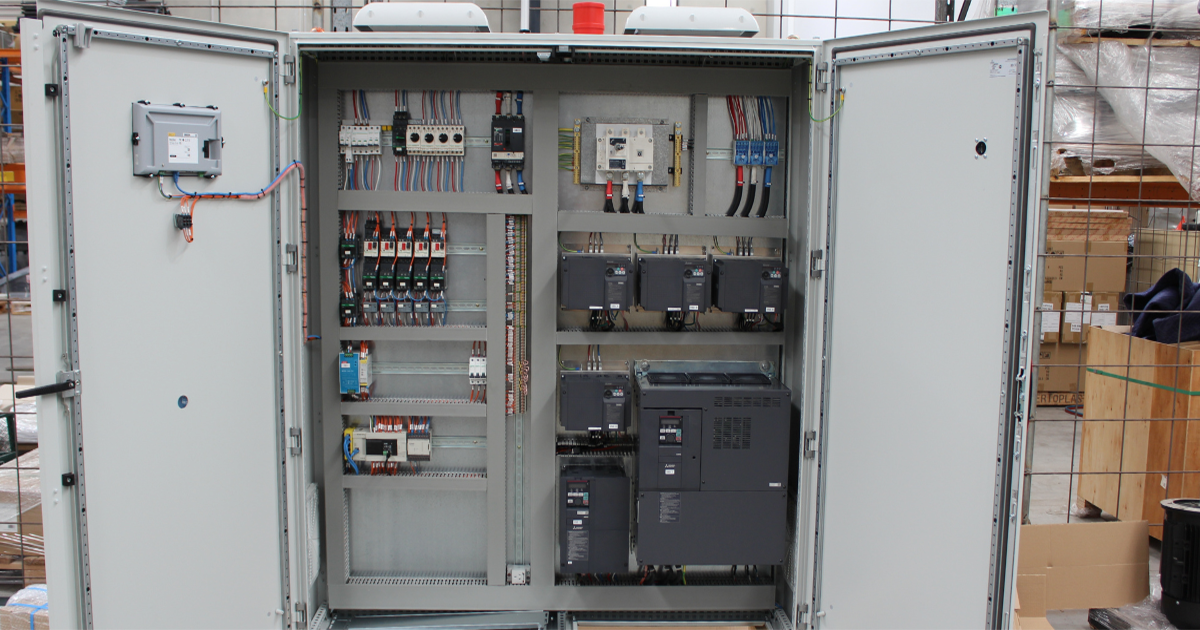
Summary
The industrial team has been hard at work completing the control panel design, construction and installation for one of our major OEM customers. Led by engineer @maxcabading, the panel design and build were completed to a high standard and moving forward will be a strong step towards waste reduction for the end user’s site. These systems have been developed to separate products from packaging and reduce landfill volumes by over 95%. They also allow the reuse of materials in the most efficient way with a waste stream purity of up to 99%.
Panel Build Details
The industrial control panel team has been busy on a number of projects including the recent panel construction, programming and commissioning of a depackaging machine for a major OEM client based in Melbourne. This particular project will be installed in Central NSW with the system being used by a soil conditioning and agriculture products company. By utilising this technology the end-user will be able to accept organic waste streams from supermarkets, efficiently removing the packaging, and granulating the material in preparation to be composted down and blended into a saleable product for agriculture.
On this project, the Teoma team provided all automation and electrical services from design through to final on-site commissioning assistance. The in-house engineering team handled all initial programming of the system confirmed via FAT (Factory Acceptance Test) with final onsite commissioning occurring interstate via remote access. Interestingly, the remote access system as provided allows real time data collection, diagnostic and optimisation support for the client into the future. On a site that is accepting a variety of materials, this ongoing support for optimisation will be highly advantageous in achieving maximum recovery rates.
Panel Build Details
Depacking and separation of waste streams is an established but rapidly growing solution across a large number of industries enabling the reduction in waste volume to landfills. Depackaging systems support the end user by allowing the bulk processing of a waste product by removing cartons, boxes, bags, bottles or even in some instances, the paper backing from plasterboard. By removing packaging efficiently the waste volume can be reduced to the net amount of the packaging with the remaining materials being sent for further processing or immediate re-use by industry.
Waste can be generated for any number of reasons ranging from faults in production to out of date products in a supermarket setting. It is of a higher social benefit to see material recovered and repurposed rather than sent for decomposition in a traditional landfill. As many people are aware, packaged food products are not suitable for traditional recycling. Removing the contents and reducing the waste only to the packaging there is a higher chance of recycling being achieved. These depackaging systems are becoming more prevalent and exist as an almost complementary system to already existing lines. With the addition of a depackaging machine, a processor is able to branch out offering complimentary processing services to their existing customer base.
Teoma have a dedicated team with a high level of design experience that is able to facilitate OEM projects from concept to completion. The added benefit of in-house design, panel build, and commissioning teams becomes vividly apparent with complex projects. As many in this industry recognise, Australia’s regulatory requirements and standards are stringent and can be highly challenging with respect to offshore manufactured plant. By working with our team, our clients can have confidence in drawing on our in-house capability established over 30 years of operation in the industrial automation field. Many Existing OEM clients cite this as the reason why they continue to engage our team.
As more Australian companies and local authorities pursue net-zero targets and a transition to a truly circular economy, solutions like this will become more prevalent. Our team is fortunate to be continuously engaged at multiple layers of the waste industry from projects like this through to onsite support for operators. Projects like this not only allow our team to showcase their capabilities but also allow them to be meaningfully involved with clients in achieving their positive social outcomes.